Parallel arm on pillar for vertical tightening of 150Nm
What our Customer Envisioned:
The goal was to create a user-friendly, ergonomic tool with real-time monitoring capabilities to ensure a seamless and safe tightening process. The versatile tool attachment at the arm’s end aligned with the customer’s need for adaptability across different fasteners. Overall, the customer’s vision centered on a technologically advanced and functional solution that optimized productivity and work environment safety.


How We delivered:
Our engineering team implemented the perfect technologies to create a robust parallel arm assembly. Focus was placed on precision engineering to guarantee optimal stability, accuracy, and uniform force distribution during the tightening process. Recognizing the importance of operator convenience, we designed a user-friendly interface and smooth control for the parallel arm. This ensured that operators could easily maneuver the tool, promoting efficiency and minimizing the learning curve.
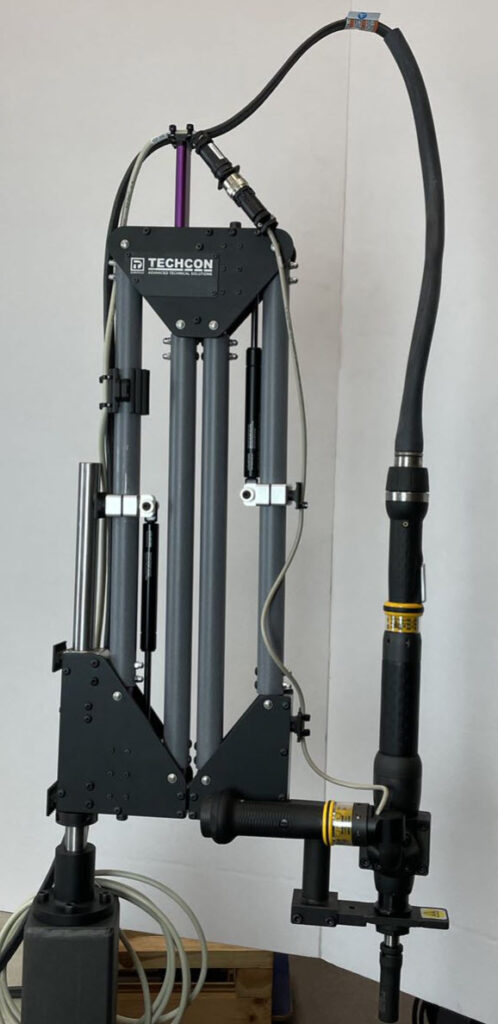
Productivity – Productivity is increased when the torque parallel arm can handle a variety of fasteners and applications. Versatility in torque settings and compatibility with different sizes and types of bolts and nuts contribute to a more efficient workflow.
Reliability – Manufacturers can enhance the reliability of torque parallel arms, providing users with a tool that consistently delivers accurate torque in a dependable manner.
Design – Designing a parallel torque arm involves careful consideration of mechanical, electrical, and ergonomic aspects to ensure optimal performance, precision, and user-friendliness.
Quality – Design, manufacturing, and quality control processes contribute to the overall quality and performance of torque parallel arms in industrial settings. Regular maintenance and adherence to recommended usage guidelines further support long-term reliability and safety.
T21457